Superando los desafíos en la fabricación de líneas de corte de acero al silicio
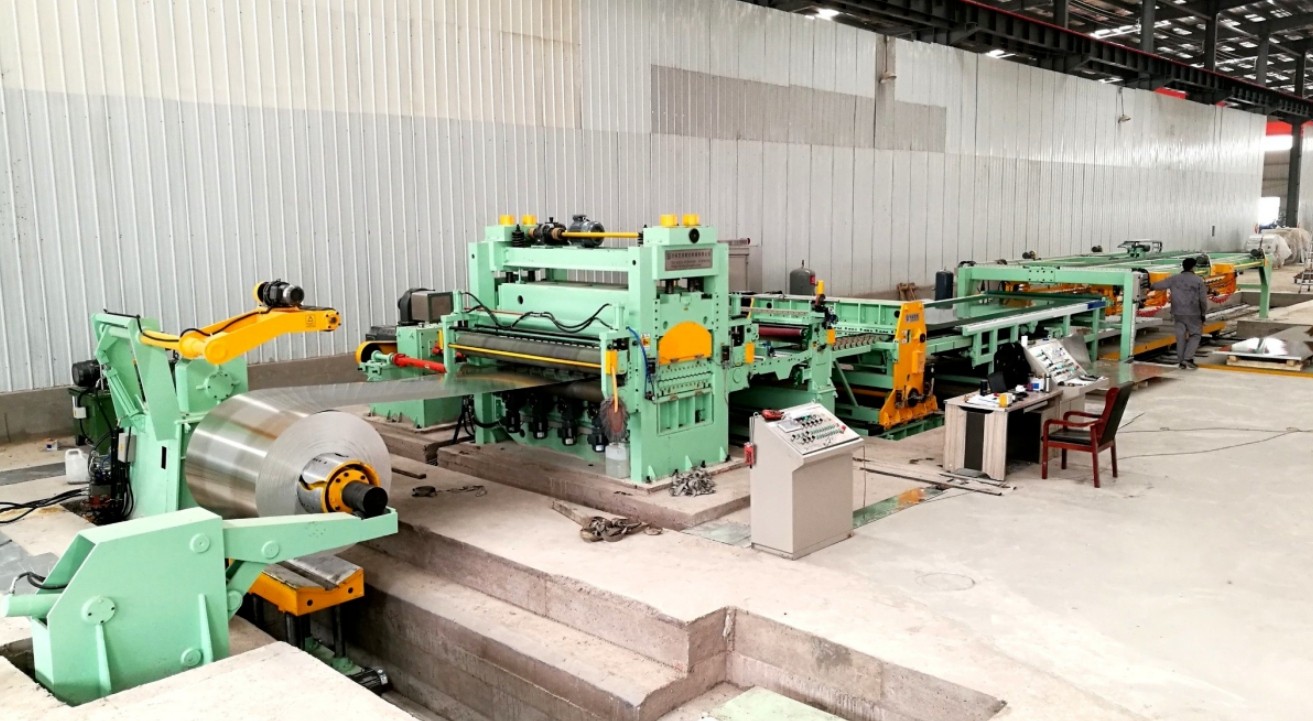
La fabricación de líneas de corte de acero al silicio implica el corte y mecanizado precisos de láminas de acero eléctrico para fabricar laminaciones para transformadores, motores y generadores. Sin embargo, pueden surgir diversos desafíos durante el proceso que afectan la productividad, la calidad y la eficiencia general. En este artículo, profundizamos en estos desafíos y exploramos estrategias eficaces para superarlos.
Comprensión de la fabricación de líneas de corte de acero al silicio
La fabricación de líneas de corte de acero al silicio es un proceso complejo que consta de múltiples etapas, como el desenrollado, la nivelación, el corte, el apilado y el cizallamiento de láminas de acero eléctrico. El objetivo es producir láminas con el tamaño y la forma exactos con un mínimo de desperdicio. Estas láminas se ensamblan posteriormente para formar el núcleo de los dispositivos eléctricos, garantizando así una conversión energética eficiente.
Desafíos que enfrenta la fabricación de líneas de corte de acero al silicio
1. Alta tasa de rechazo
Uno de los principales desafíos de la fabricación de líneas de corte de acero al silicio es la alta tasa de desperdicio. Dado que las laminaciones se cortan y conforman con precisión, cualquier imprecisión puede generar desperdicio de material. Una alta tasa de desperdicio no solo incrementa los costos de producción, sino que también tiene un impacto ambiental.
2. Corte de precisión
El corte de precisión es esencial en la fabricación de alambre de corte de acero al silicio para lograr las dimensiones requeridas y minimizar el desperdicio de material. Sin embargo, lograr una precisión constante durante todo el corte puede ser un desafío debido a factores como el desgaste de la cuchilla, la alineación de la máquina y las variaciones del material.
3. Manejo de materiales
El manejo eficiente de materiales es fundamental para mantener un flujo de producción fluido en una línea de corte. Las placas de acero grandes y pesadas requieren técnicas de manejo adecuadas para evitar daños y garantizar un posicionamiento preciso durante el corte y el apilado. El manejo inadecuado de materiales puede provocar errores, retrasos y pérdida de productividad.
4. Apagado de la máquina
El tiempo de inactividad de la máquina es un obstáculo importante para la fabricación de líneas de corte de acero al silicio. Las fallas mecánicas, los requisitos de mantenimiento y los cambios de herramientas pueden causar interrupciones inesperadas en el proceso de producción. Minimizar el tiempo de inactividad de la máquina es fundamental para maximizar la productividad y alcanzar los objetivos de producción.
5. Control de calidad
Una calidad constante durante todo el proceso de fabricación es fundamental para ofrecer equipos eléctricos fiables y eficientes. Los retos del control de calidad en la fabricación de líneas de corte de acero al silicio incluyen la detección de defectos, la supervisión de la precisión dimensional y la garantía de la uniformidad de la laminación. Un control de calidad inadecuado puede provocar fallos en el producto y la insatisfacción del cliente.
6. Cuestiones ambientales
La fabricación de líneas de corte de acero al silicio tiene un impacto ambiental debido a la generación de residuos, el consumo de energía y las posibles emisiones. Es fundamental que los fabricantes adopten prácticas sostenibles que minimicen los residuos, el consumo de energía y el impacto ambiental.
Superando desafíos
1. Mejorar la tasa de desperdicio
Para reducir las tasas de desperdicio, los fabricantes pueden emplear técnicas de corte avanzadas y sistemas de medición de precisión. El uso de una máquina de corte láser con un sistema de monitoreo y control en tiempo real permite lograr un corte preciso y minimizar el desperdicio de material. Además, la optimización de los algoritmos de anidamiento para aumentar el aprovechamiento del material y la implementación de un mantenimiento proactivo pueden mejorar aún más las tasas de desperdicio.
2. Mejorar la precisión del corte
El mantenimiento regular de las herramientas de corte, como el afilado o el cambio de cuchillas, garantiza una precisión constante. La implementación de un sistema automatizado de detección del desgaste de las cuchillas puede generar alertas oportunas para su reemplazo. Los sistemas avanzados de control numérico computarizado (CNC) también pueden mejorar la precisión de corte al compensar las variaciones de material y la desalineación de la máquina.
3. Simplificar el manejo de materiales
Invertir en sistemas automatizados de manipulación de materiales, como brazos robóticos o cintas transportadoras, puede reducir los errores humanos y aumentar la eficiencia. El uso de sistemas de código de barras o RFID para rastrear e identificar placas de acero puede simplificar las operaciones de manipulación de materiales. La capacitación adecuada de los operadores en técnicas de manipulación también puede ayudar a aumentar la productividad y reducir los errores.
4. Minimizar el tiempo de inactividad de la máquina
Implementar programas de mantenimiento preventivo, tecnologías de mantenimiento predictivo y sistemas de monitoreo de condición puede minimizar el tiempo de inactividad de las máquinas. Inspeccionar, lubricar y calibrar las máquinas regularmente ayuda a identificar posibles problemas y prevenir averías inesperadas. Además, mantener un inventario de repuestos garantiza un reemplazo rápido y minimiza el tiempo de inactividad.
5. Implementar un control de calidad eficaz
Mejore el control de calidad con tecnologías de inspección avanzadas, como sistemas de visión artificial y métodos de ensayos no destructivos. La monitorización en tiempo real de la precisión dimensional y la uniformidad de la laminación garantiza el cumplimiento de las especificaciones. La implementación de técnicas de control estadístico de procesos y un programa integral de aseguramiento de la calidad también contribuye a una calidad constante del producto.
6. Abordar los problemas ambientales
Los fabricantes pueden implementar prácticas sostenibles para reducir el impacto ambiental de la fabricación de líneas de corte de acero al silicio. Esto incluye optimizar el consumo de energía mediante equipos eficientes, reciclar residuos e implementar medidas de control de la contaminación. El cumplimiento de las normativas y certificaciones ambientales demuestra aún más el compromiso con la fabricación sostenible.
En conclusión
La fabricación de líneas de corte de acero al silicio se enfrenta a diversos desafíos que pueden afectar la productividad y la calidad. Al comprender y abordar eficazmente estos desafíos, los fabricantes pueden optimizar sus procesos y mejorar el rendimiento general. Mediante la implementación de tecnologías avanzadas, la simplificación del manejo de materiales y la priorización del control de calidad y la sostenibilidad, los fabricantes pueden superar estos desafíos y alcanzar el éxito en la fabricación de líneas de corte de acero al silicio. Si desea obtener más información sobre las líneas de corte de acero al silicio o adquirirlas, contáctenos .
Hengli es un fabricante profesional de equipos de corte de acero al silicio a medida en China. Basándonos en conceptos industriales modernos y una excelente tecnología de automatización, nuestros productos principales incluyen un sistema automático para el estampado y conformado de paneles exteriores de automóviles, robots en línea, dispositivos de corte automático de chapa metálica de alta precisión, sistemas de detección automática industrial en línea, dispositivos de automatización de energía eléctrica y sistemas de control automático. Una solución integral. Nuestros productos principales están sincronizados con la tecnología más avanzada del mundo y se utilizan ampliamente en industrias clave de la economía nacional, como la fabricación y el procesamiento de piezas de automóviles, el procesamiento de acero y metalurgia, la energía eléctrica y el embalaje metálico.